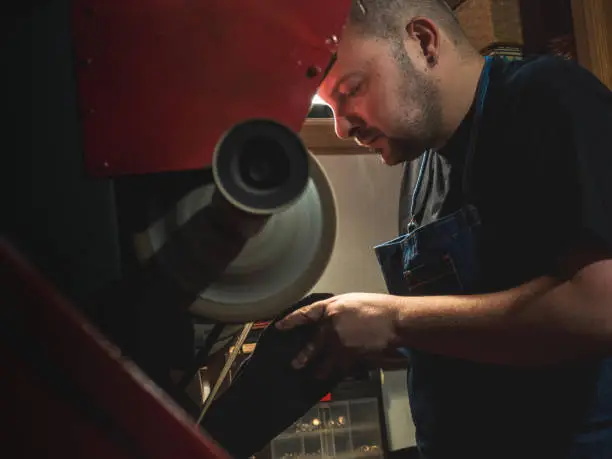
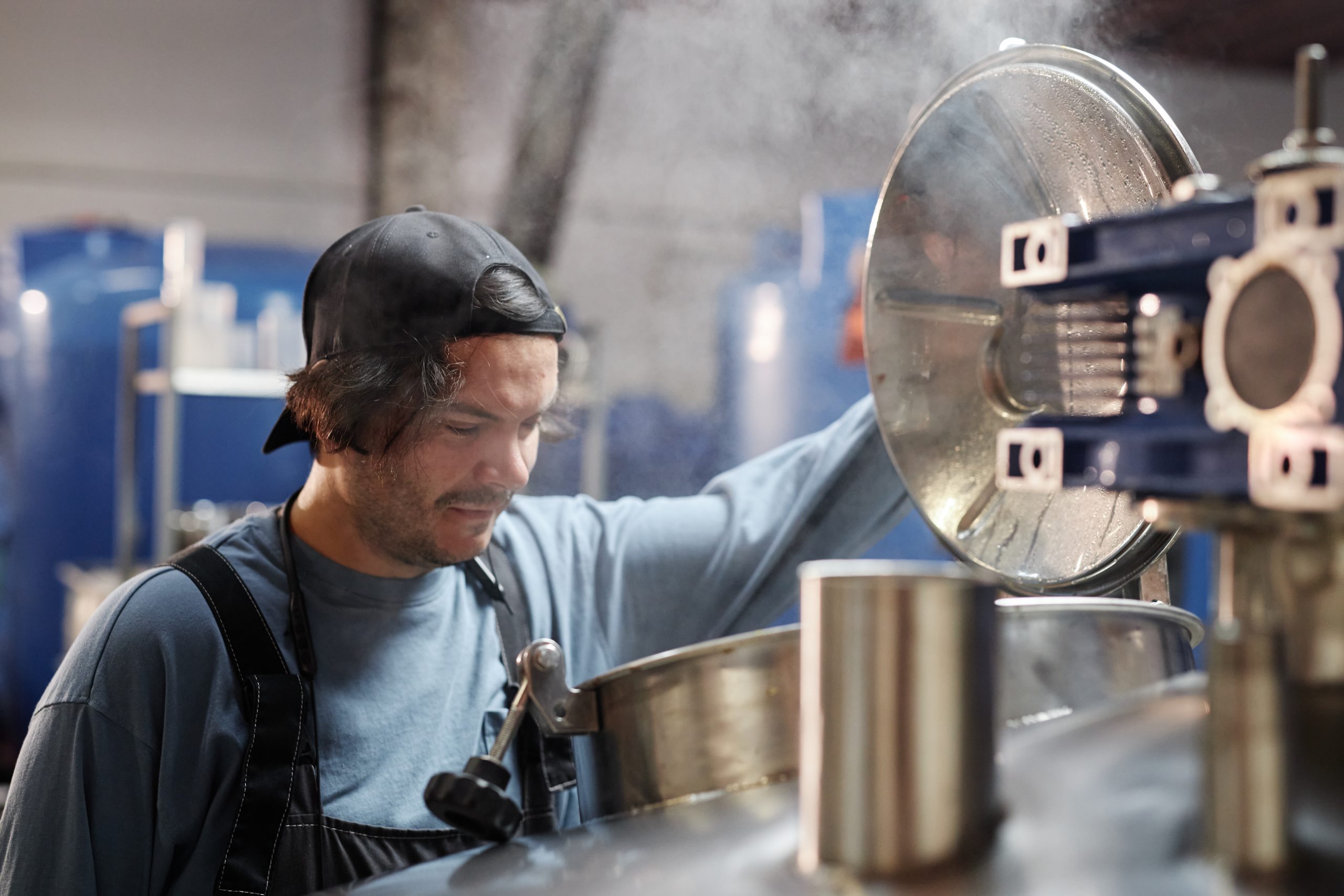
How Metal Spinning Can Help Reduce Manufacturing Costs
In today’s competitive manufacturing environment, companies constantly seek ways to optimise production and minimise expenses. One technique that stands out for its cost-efficiency, flexibility, and precision is metal spinning. Whether producing prototypes or large-scale batches, metal spinning offers unique advantages that directly reduce costs across various stages of manufacturing.
At Tanfield Metal Spinners, we specialise in delivering tailored metal spinning solutions that meet stringent quality standards and provide measurable economic benefits. This blog explores how metal spinning can significantly lower manufacturing costs without compromising performance or design complexity.
Reduce Tooling Expenses with Metal Spinning
One of the most immediate and impactful cost savings offered by metal spinning is in tooling. Traditional forming methods, such as stamping or casting, typically require expensive, intricate dies and moulds. These tools can take weeks to produce and may need full replacement with each design iteration, which adds time and considerable expense, particularly in the prototyping stage.
In contrast, metal spinning uses simple mandrels or forming tools that are significantly more cost-effective. These tools are quicker to manufacture, easier to modify, and ideal for projects with changing specifications. This flexibility makes metal spinning especially attractive for bespoke or small-to-medium volume runs where adaptability and affordability are key.
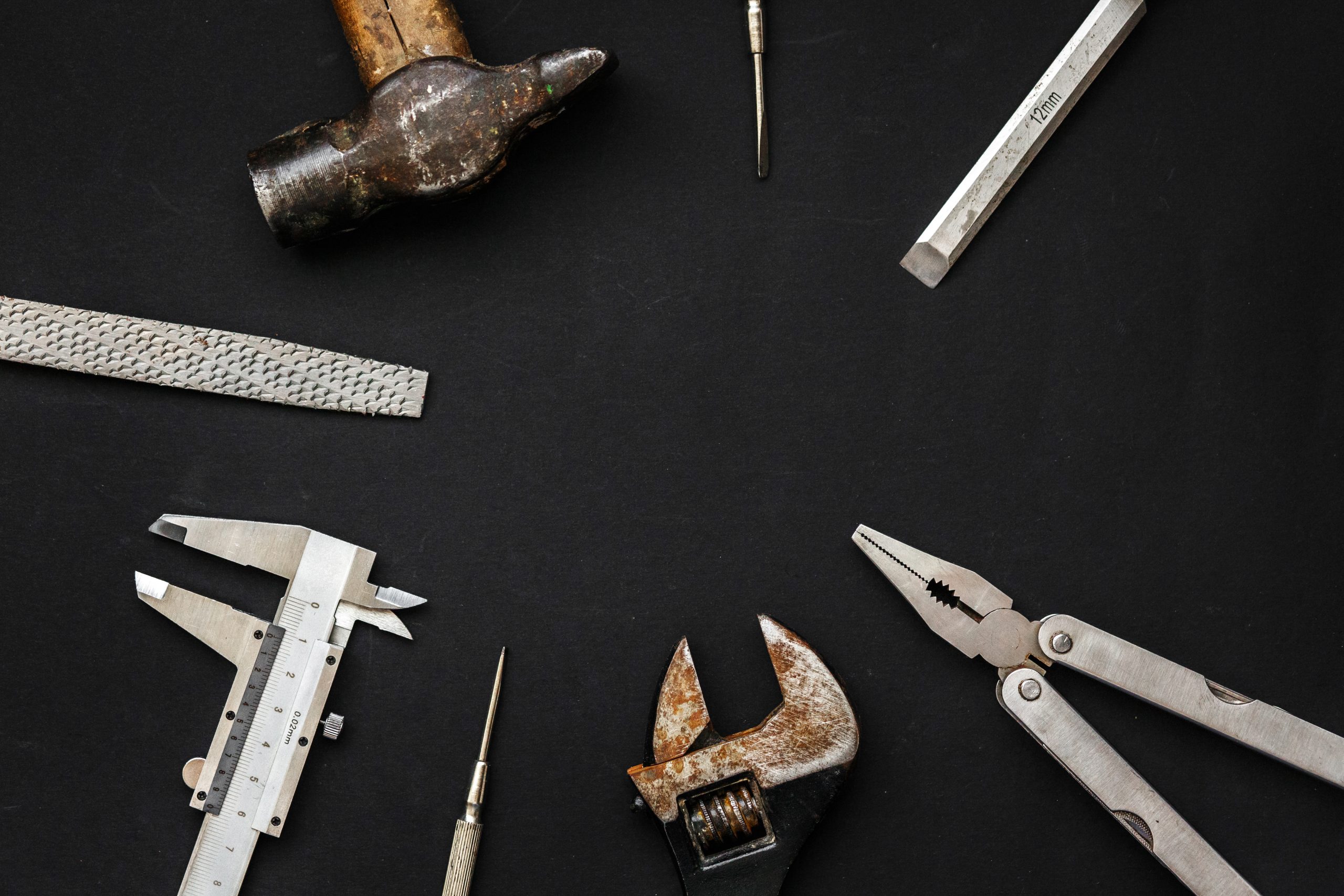
Minimise Material Waste in Manufacturing
Subtractive methods, such as CNC machining, cut away large portions of raw material. However, metal spinning is a displacement process, which means it reshapes the metal rather than removing it, resulting in minimal waste.
Reduced waste doesn’t just mean a smaller environmental footprint; it translates directly to financial savings. Material costs often comprise a significant portion of overall manufacturing expenses, especially when working with high-value metals like stainless steel, aluminium, or copper. By maximising material use, metal spinning ensures you get more from every sheet or blank of metal.
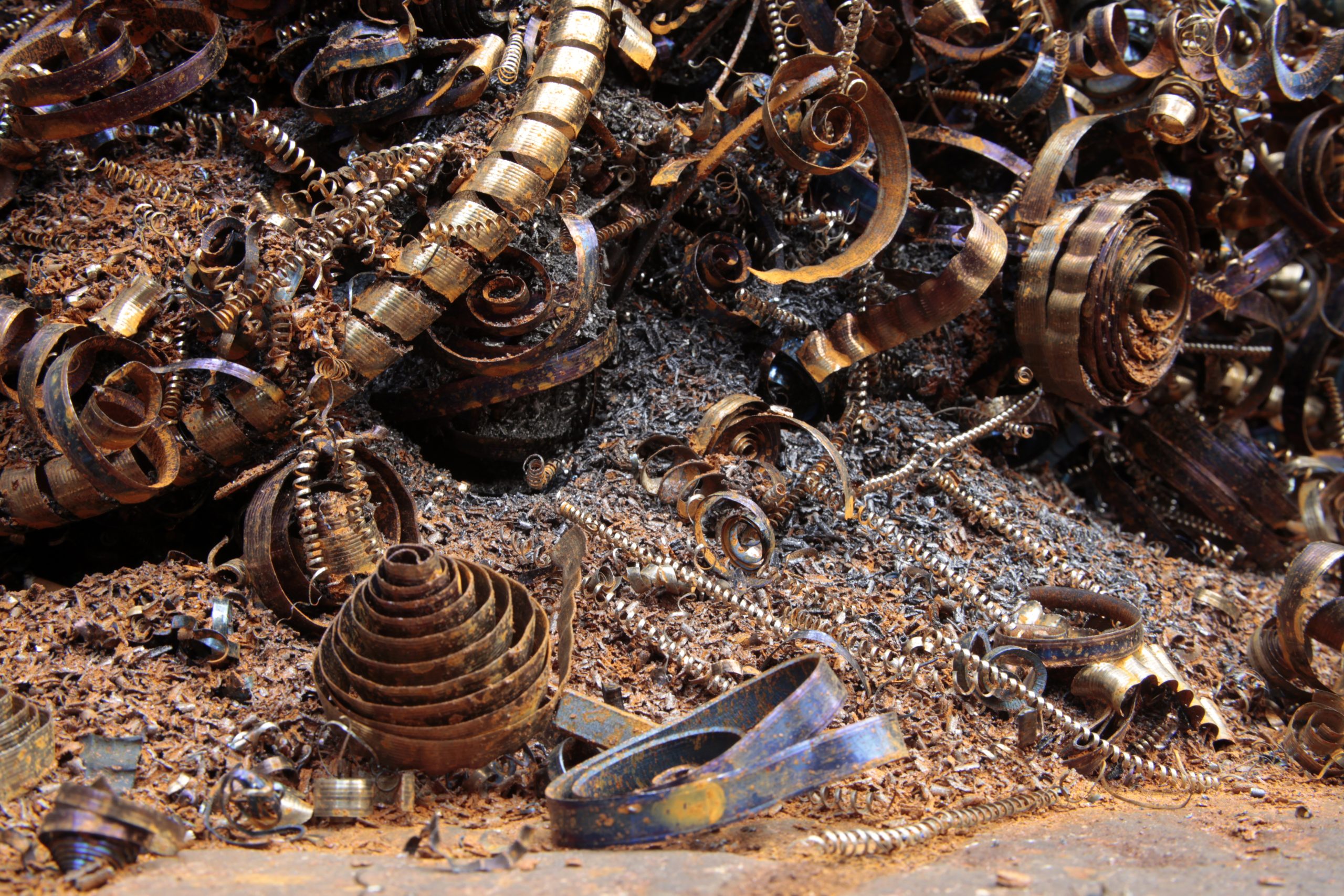
Increase Production Speed and Reduce Labour Costs
Thanks to advances in CNC-controlled spinning, modern metal spinning has become an efficient process capable of producing complex parts with consistent accuracy. These automated systems can operate continuously with minimal human intervention, significantly reducing production time and labour costs.
Compared to manual fabrication, CNC metal spinning increases repeatability and speed, allowing manufacturers to meet tight deadlines and scale production quickly without compromising quality. For high-volume manufacturing, this efficiency equates to a lower cost per unit.
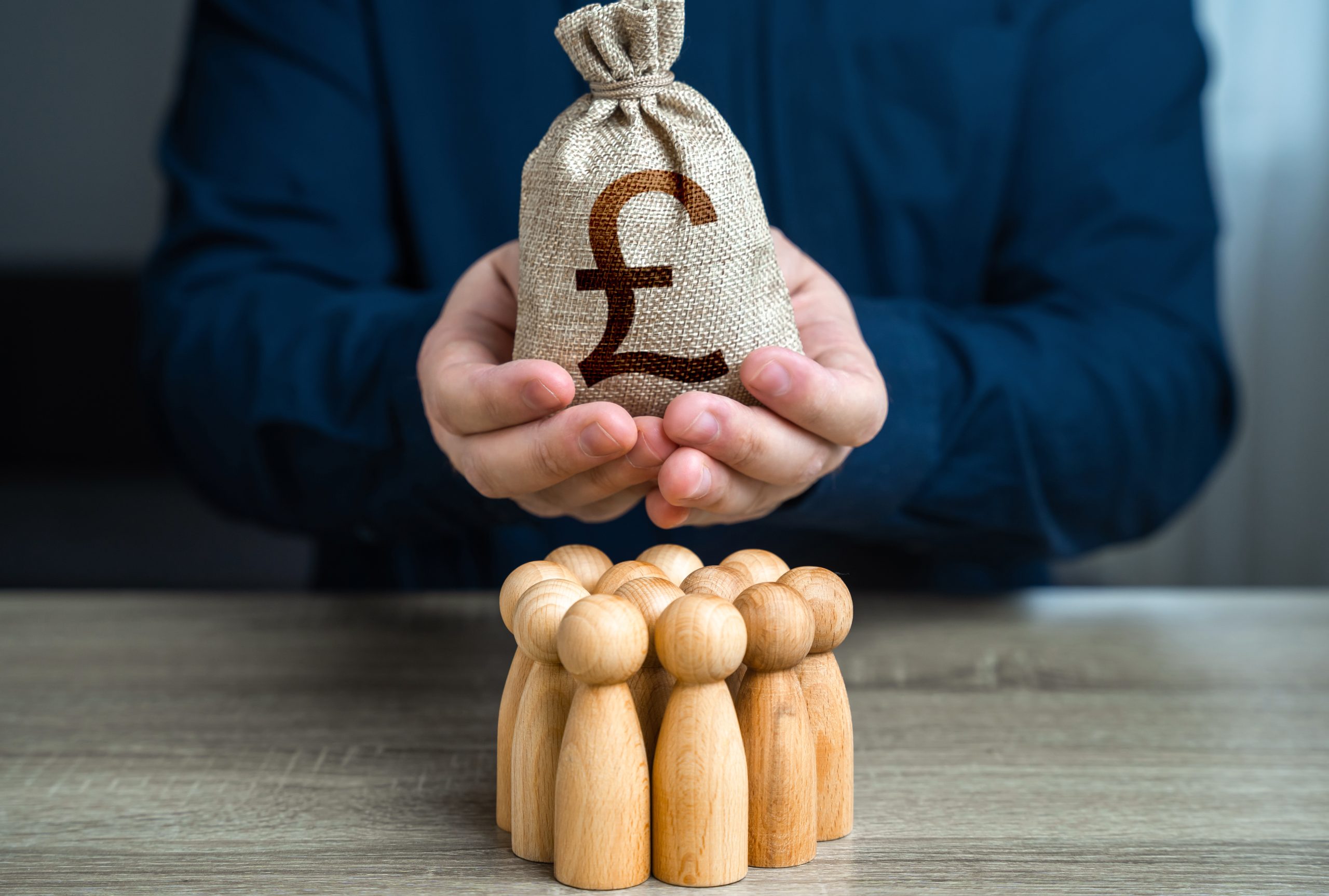
Improve Design Flexibility and Responsiveness
One of the standout advantages of metal spinning is its ability to accommodate a wide range of shapes, sizes, and materials. Spinning allows for seamless and symmetrical results whether the project needs shallow domes, deep cylinders, or intricate contours.
This flexibility is especially valuable during product development, where design changes are often necessary. Traditional fabrication methods may require new dies or tooling for each variation, which can be costly and time-consuming. In contrast, metal spinning allows for quick modifications with minimal impact on the overall budget, enabling faster turnaround and reducing the financial risk of experimentation.
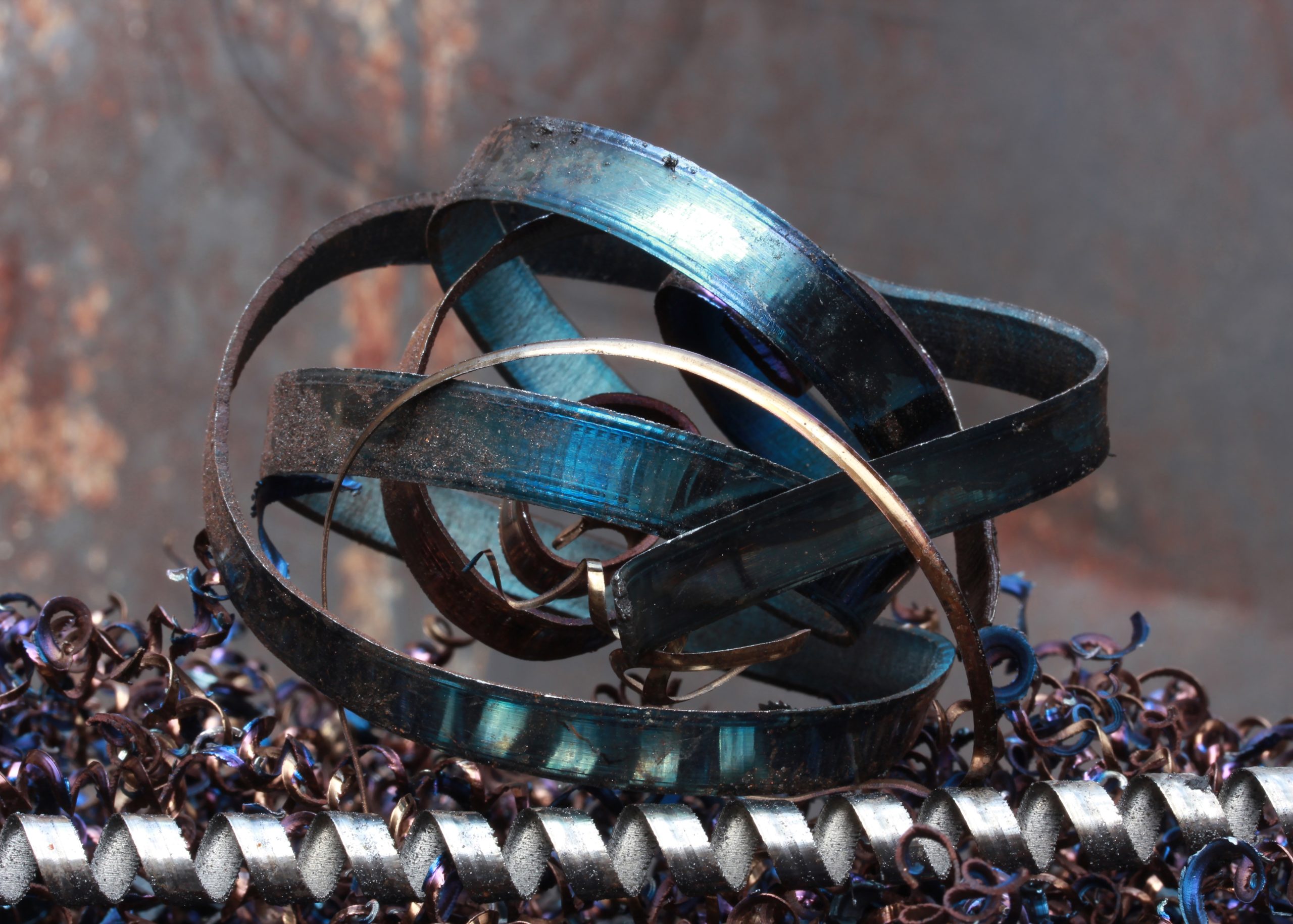
Enhance Part Strength Without Extra Processing
Metal spinning not only shapes the material but also enhances its mechanical properties. The process introduces a work-hardening effect, increasing the component’s tensile strength and resistance to deformation. As a result, parts manufactured through spinning are inherently more durable and often do not require additional reinforcement or post-processing steps.
This strength makes spun parts ideal for high-performance applications in industries such as aerospace, automotive, and energy, where durability and reliability are critical. Eliminating extra processing steps further reduces production costs and shortens lead times.
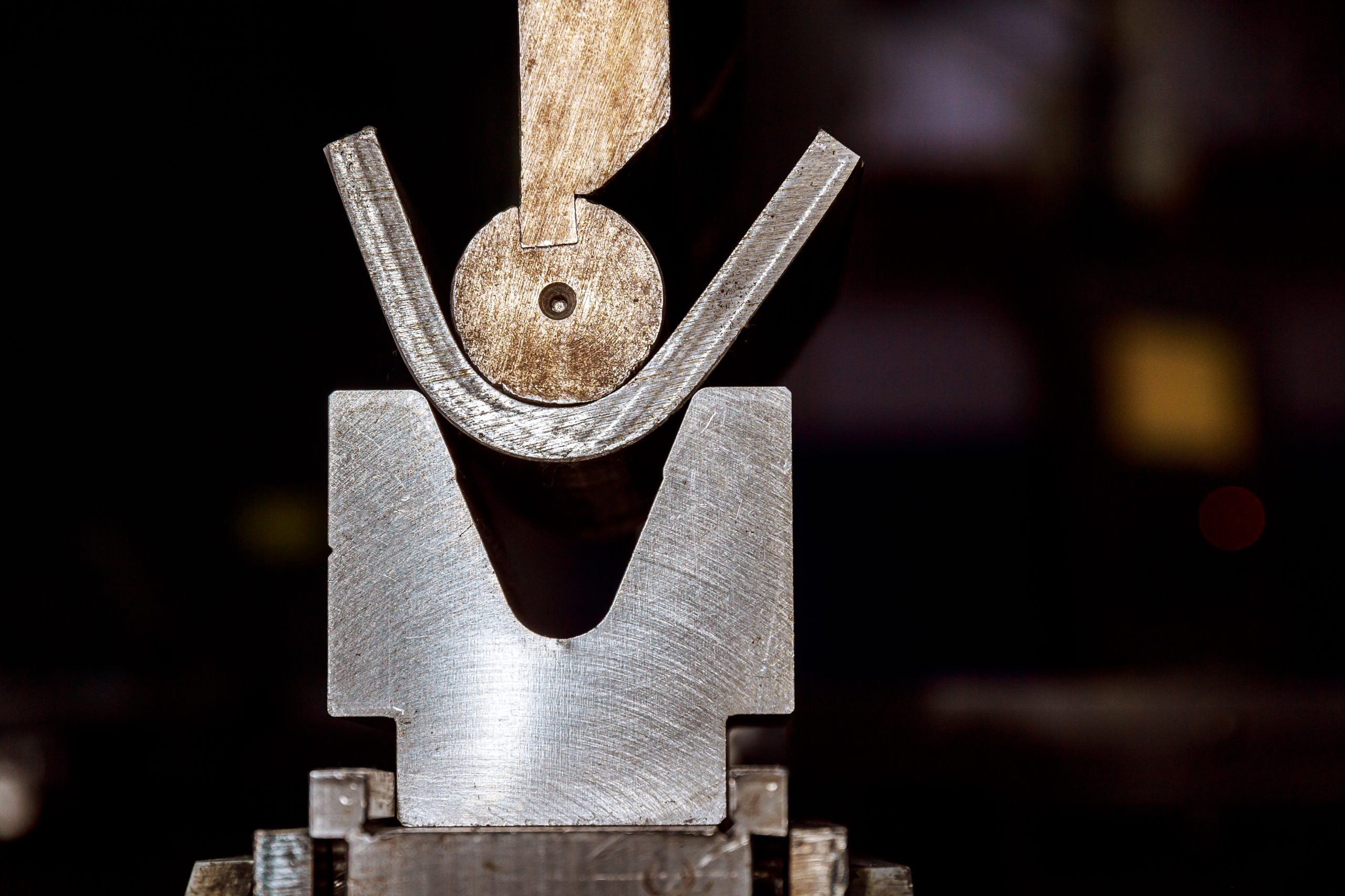
Lower Unit Costs with Scalable Production
While metal spinning is often celebrated for its suitability in small batches and custom orders, it also performs exceptionally well in large-scale production. Automated CNC spinning equipment enables manufacturers to produce thousands of identical components with minimal deviation.
When combined with low tooling costs and reduced waste, metal spinning offers a highly cost-effective solution for mass production. The more units produced, the greater the cost savings per part, especially compared to forming methods with high fixed setup costs like stamping or casting.
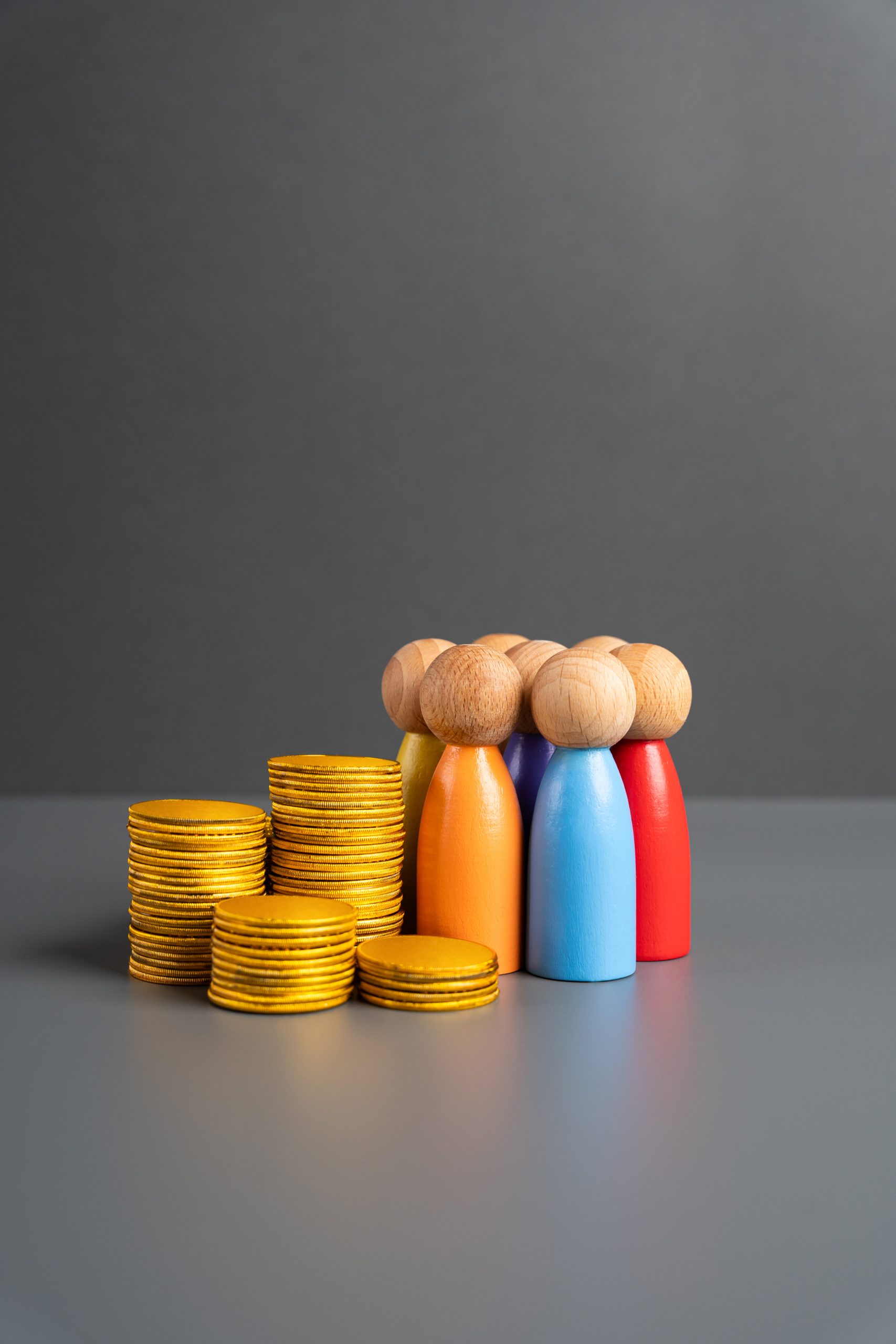
Reduce Assembly Time by Using Fewer Components
Metal spinning produces seamless parts that often combine multiple design features into a single, integrated component. This factor reduces the need for welding, joining, or assembly of multiple parts, which cuts down on labour costs and reduces the chances of component failure or alignment issues.
In essence, one spun part can replace two or three fabricated pieces, streamlining the production process and eliminating unnecessary costs in assembly and inspection.
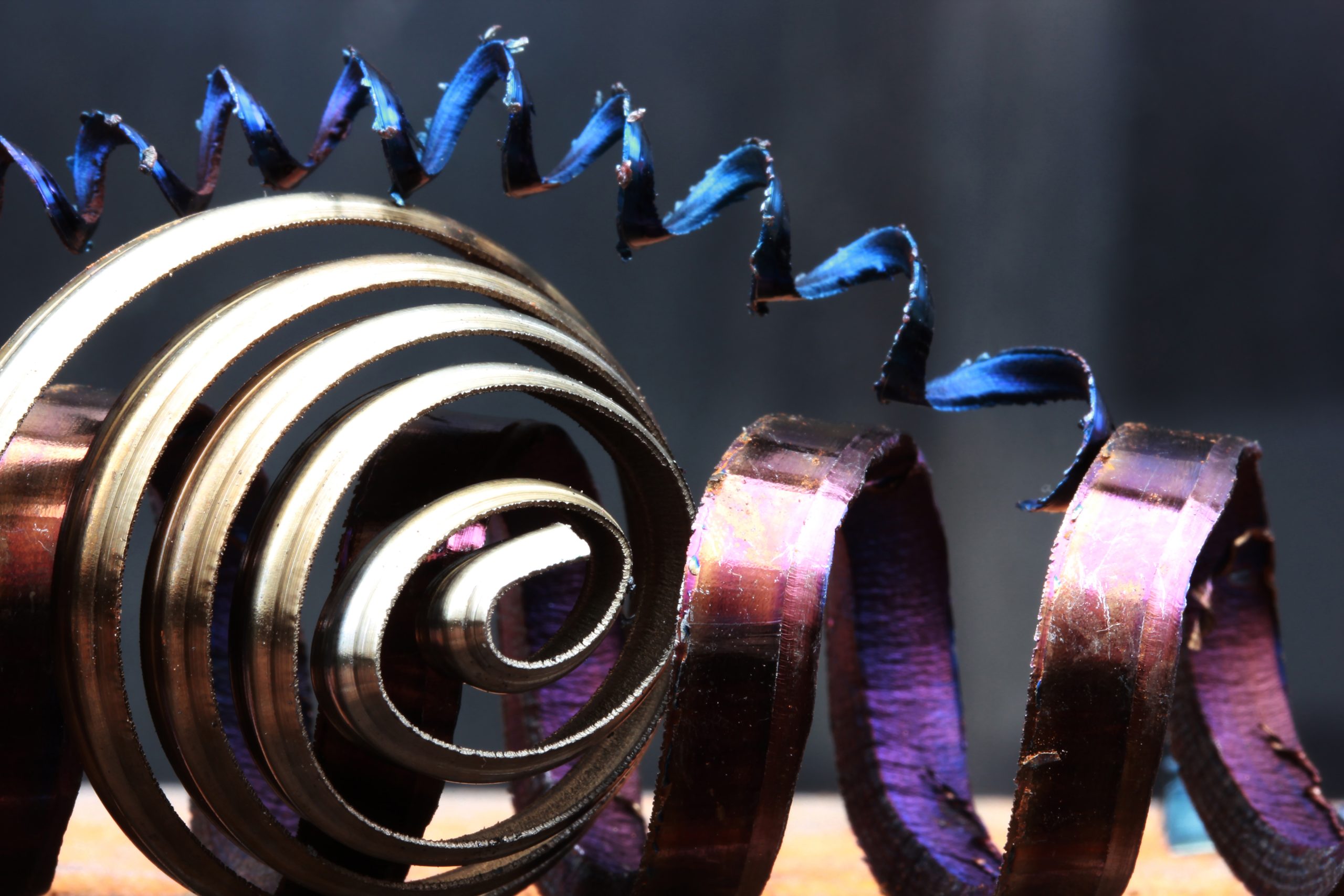
Control Surface Finishing and Polishing Costs
Though spinning naturally produces a smooth finish, additional metal polishing can elevate the surface quality to meet aesthetic or functional standards. Because spun parts have fewer welds and seams, polishing is typically more straightforward, resulting in faster finishing times and lower polishing costs.
At Tanfield, our in-house polishing capabilities ensure that components meet both visual and technical specifications while keeping post-processing time and expense to a minimum.
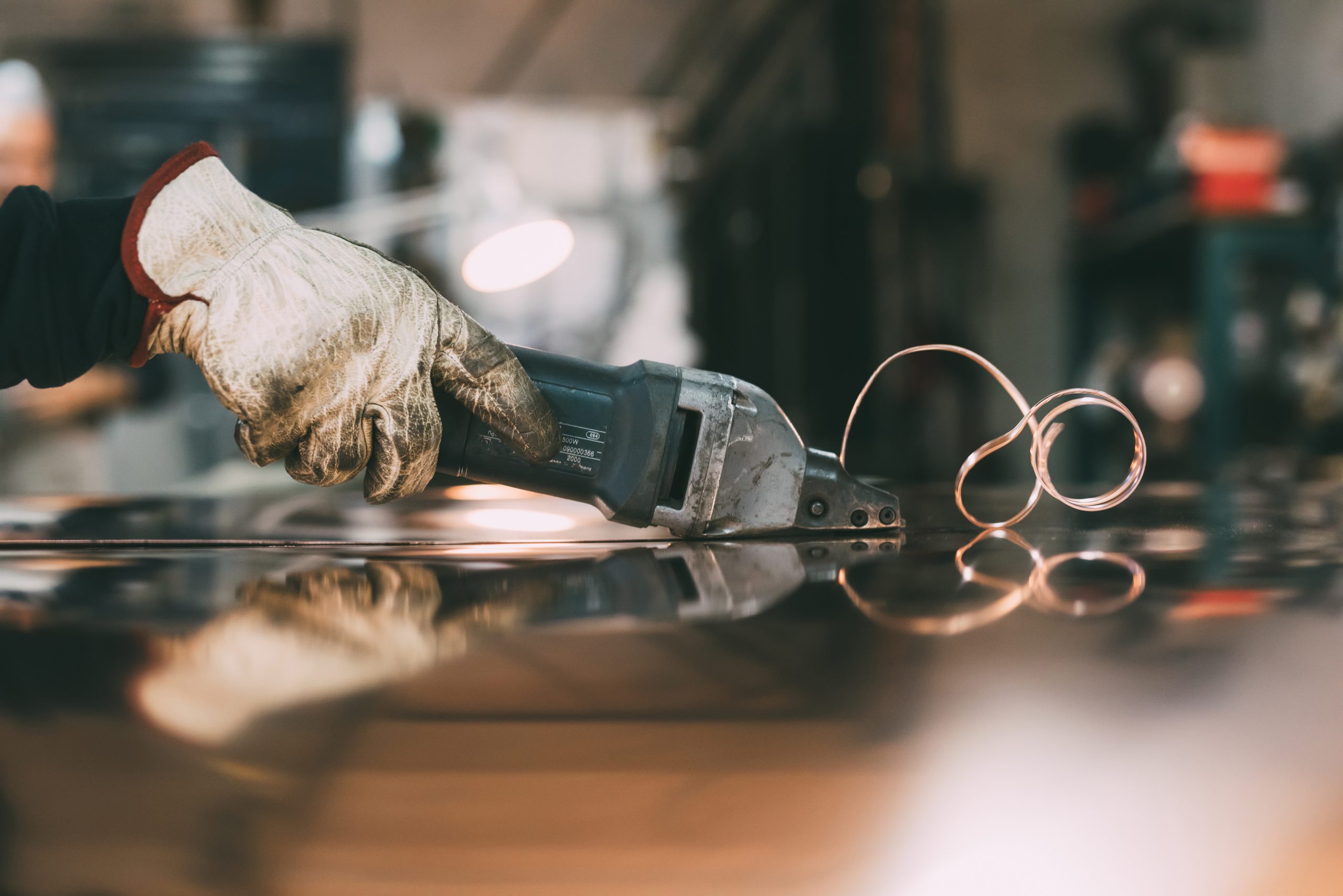
Adopt a More Sustainable, Cost-Saving Manufacturing Process
Incorporating sustainable manufacturing practices is not just an ethical decision but a financial one. Metal spinning is inherently more sustainable than many alternative processes due to its low waste, energy efficiency, and compatibility with recycled materials.
Sustainability leads to long-term savings by reducing material costs, lowering energy consumption, and aligning with environmental regulations that may otherwise incur fines or penalties. In a world increasingly focused on ESG (Environmental, Social, and Governance) performance, these savings are both financial and reputational.
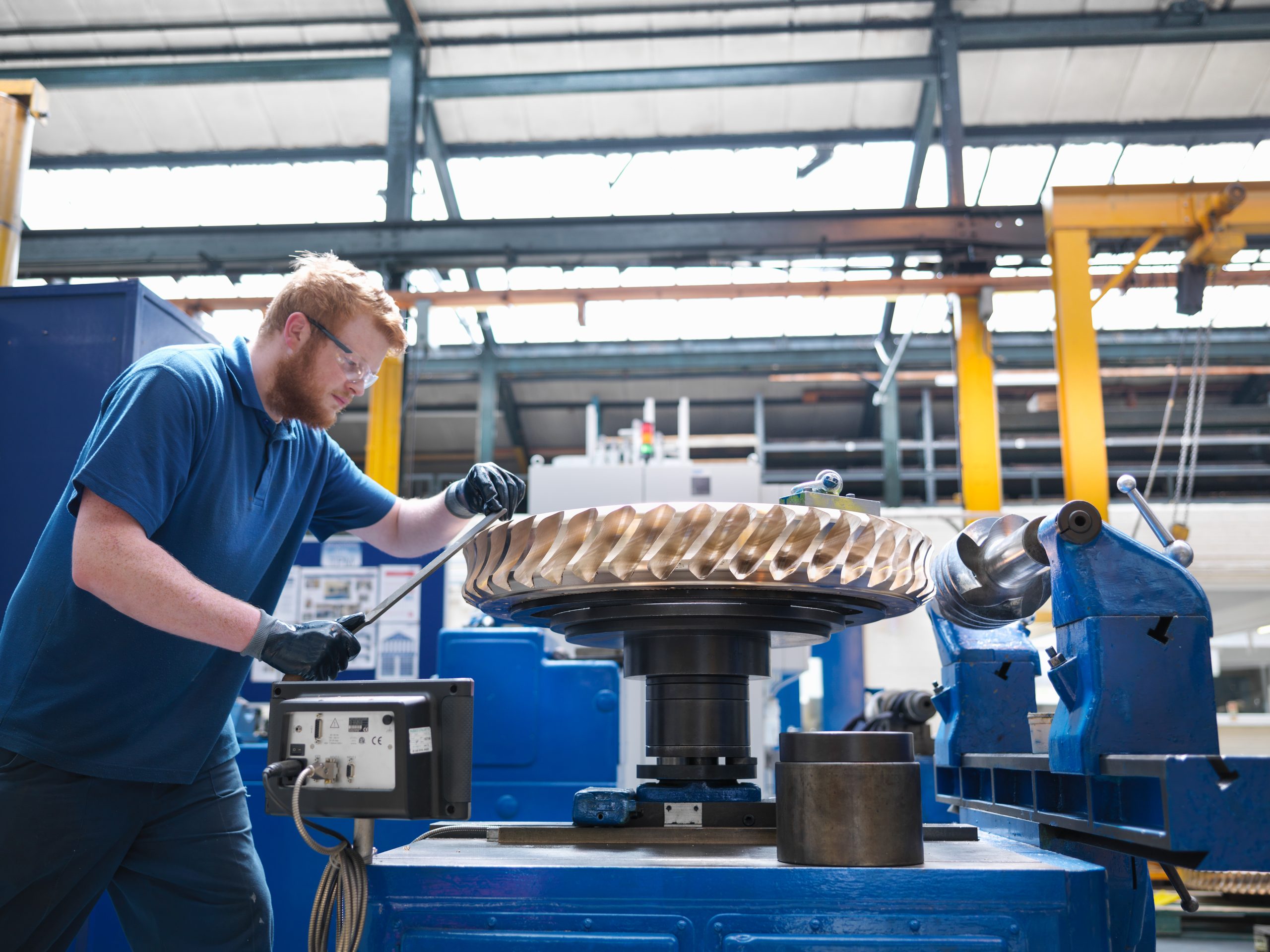
Metal Spinning is a Smarter Way to Cut Costs in Manufacturing
From design to delivery, metal spinning offers a comprehensive suite of cost-saving advantages that benefit manufacturers across a range of sectors. By reducing tooling and material costs, increasing production efficiency, and enabling fast, flexible prototyping, the process delivers a clear return on investment, especially when executed with the precision and expertise of a specialist like Tanfield Metal Spinners.
Whether you’re developing a new product or looking to optimise an existing one, metal spinning offers an efficient and economical solution that meets both budgetary and technical demands.
Ready to reduce your manufacturing costs? Contact Tanfield Metal Spinners today to explore how our bespoke spinning services can support your next project.
Contact Us Today!
We encourage you to reach out to us today, our team of knowledgeable experts is ready to answer your questions, provide personalised guidance, and help you find the right solution for your needs.
Contact Us